- Group
- 2019
- 2 Weeks
- Arduino, CNC, 3D Printing
- Tangible Interaction
This project was done during diploma course ‘How to make (almost) anything’ as graduation project, a digital prototyping diploma program taught by Neil Gershenfeld, Director at Center for Bits and Atom, MIT. This program helps to exposes to over 20 skills over 20 weeks including Web Design, Machine Design, Project Management, Electronic Design, 3D Scanning and Printing, Embedded Programming, etc. These skills are then showcased through the ‘Graduation Project’.
This project was a group project done during the week titled ‘Machine Design Week’ split over two weeks. We made an LED Maze which can be controlled using accelerometer or joystick. It used dual axis mechanism. and the movement in Z axis was primary in this case.
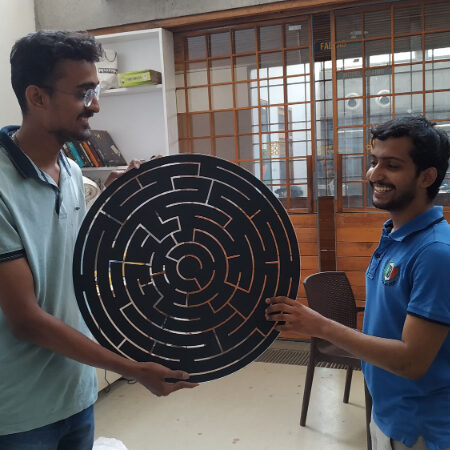
Mechanism
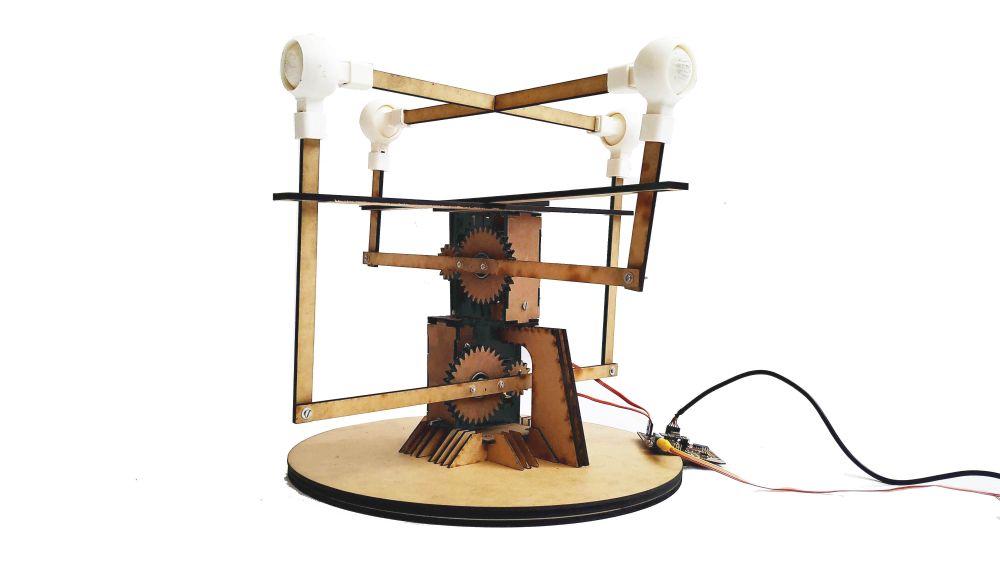
Features :
- 2 axis mechanism
- Includes Ball socket joints
- 20:10 Gears, Module: 2, Pressure Angle: 25
- Weight carrying capacity : Around 4 kilos
- Fasteners : self locking mechanism and bolt
Components

2:1 Servo Drive System : MG995 Servo | Laser Cut Involute Gears | 20:10 Gears, Module: 2, Pressure Angle: 25
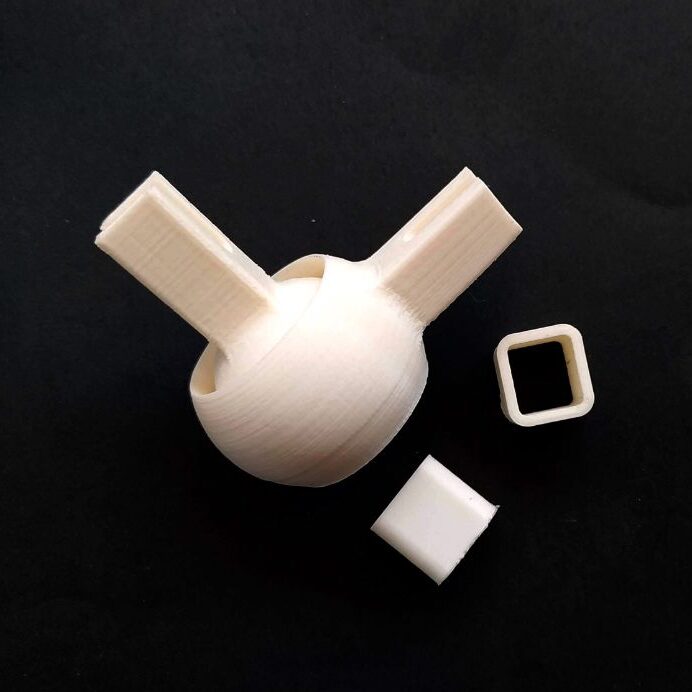
Ball Socket Joints : 3D printed with ABS | Interlocking Mechanism | 4 degree freedom of movement
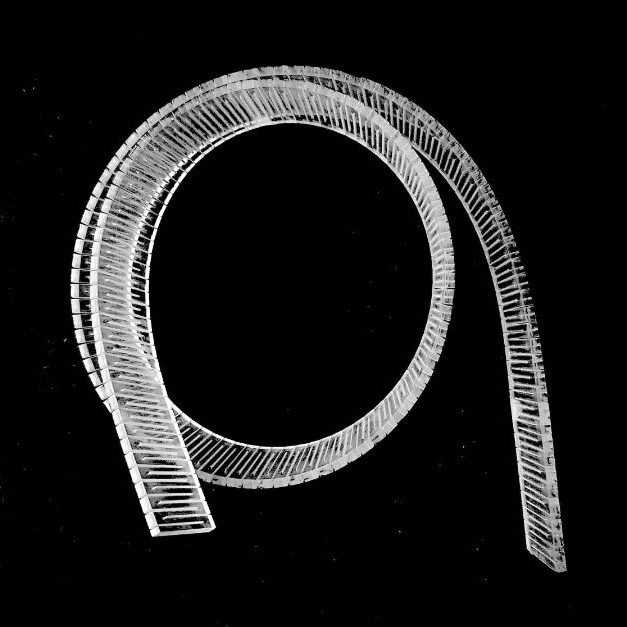
Acrylic Walls bent using Laser Kerf : 5mm thickness | Parametrically generated living hinges | Edge lighting used to illuminate the entire structure
Electronic Components
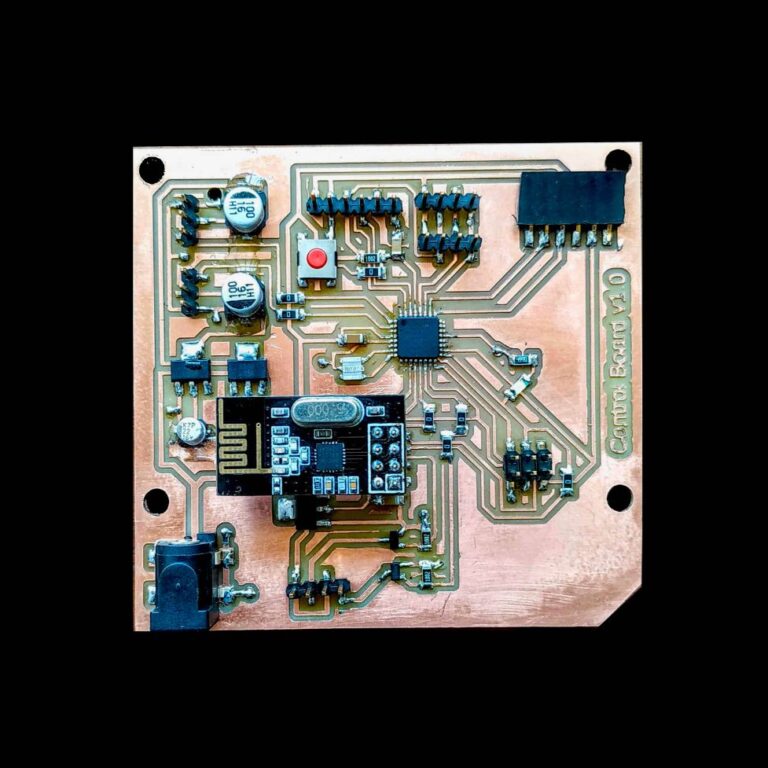
Main Board : Atmega328p running at 20MHz 5v | Seperate power channelf or each MG995 Servo using lm2940 | nrf24l01 for communication | Dual channel LED strip control using ADS355AN mosfets.
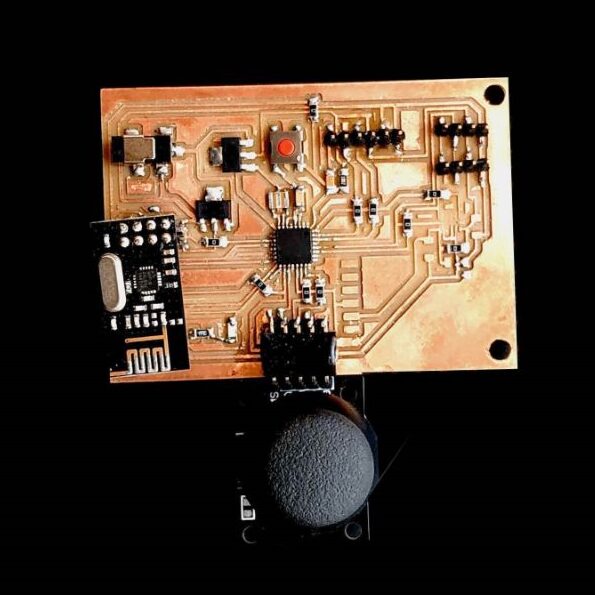
Joystick Controller : Joystick Module | Atmega328p running at 8MHz, 3.3v in low power mode | nRF240l01 for communication.
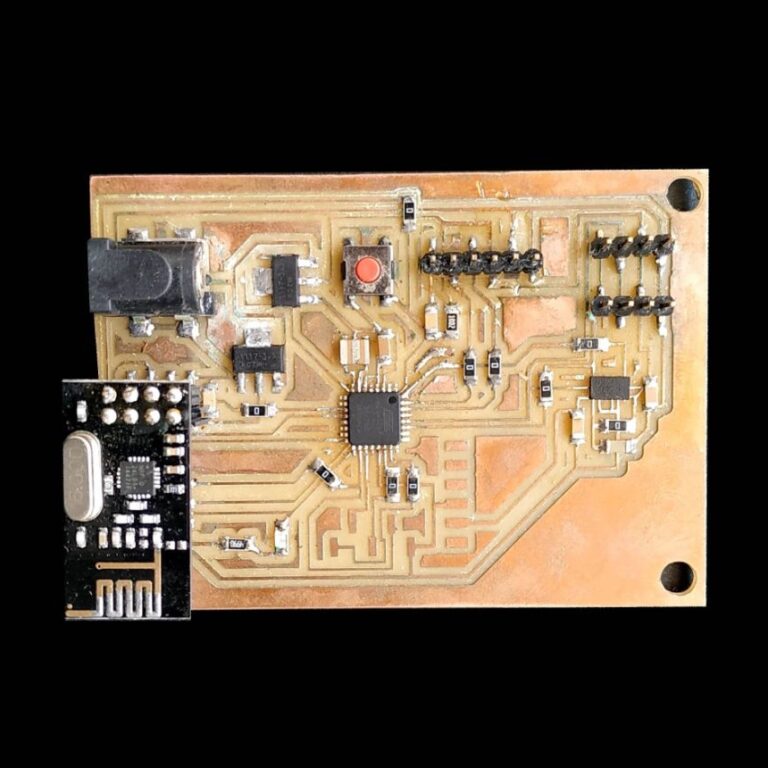
Gesture Controller : ADXL345 accelerometer in i2c | Atmega328p running at 8MHz, 3.3v in low power mode | nRF240l01 for communication.